Procurement and Supply Chain Management Made Simple
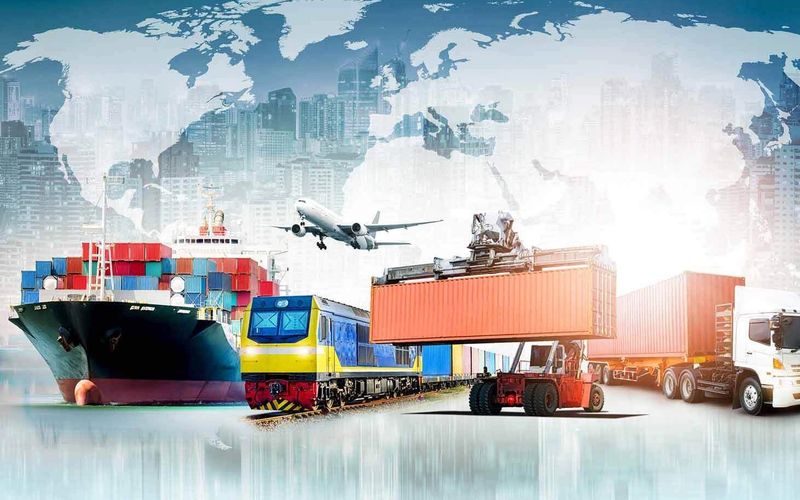
Increasing sales, profitability and customer service through the eradication of commercial costs, waste and risks.
Increasing sales, profitability and customer service through the eradication of commercial costs, waste and risks.
An organisation's most prominent issue is translating its strategic intent into the tactical and operational plans required to establish and achieve its goals and objectives. There is a perception that leaders only exist at the higher levels of management. However, a truly effective organisation understands that leaders exist at all levels, critically translating a strategic vision into action.
A procurement function negotiates terms with suppliers to eradicate commercial, legal, and safety risks and maximise customer satisfaction and service. However, management risks can threaten an organisation's ability to achieve its goals. Commercial risks are centred on an organisation's trading plans, which may not turn out as originally planned.
Supply chains can vary in length and complexity depending on the specific industry and sector they operate in and the end user's demands. By allowing supply and demand to function independently, supply chains reduce costs, expedite economies of scale, and maximise productivity. Within the supply chain, organisations specialise in value-adding activities that provide a competitive advantage in the supply of products and services essential for their mutual existence.
Procurement negotiate terms with suppliers to eradicate commercial, legal, and safety risks, to maximise customer satisfaction and service. A procurement function operates a negotiating process that has the authority to procure products and service on behalf of an organisation, and may operate as a separate, discrete function but are often dispersed within operational teams throughout the supply chain to manage the risk aspects of purchasing.
The concept of "efficiency" in logistics requires further clarification. Some interpret it as reducing costs, waste, and time in material flow. In contrast, others see it as maximising customer service, with cost management being essential but not at the expense of customer satisfaction. It is crucial for the logistics strategy to align with the organisation's mission statement, sales policy and customer service strategy, to meet customer needs efficiently and effectively at a reasonable cost.
The primary function of warehousing is to regulate and effectively manage the flow of goods, ensuring that demand is met without any disruptions in supply. The size, scope, geographic location and functionality of warehouses varies significantly, ranging from massive structures capable of handling a high volume of inbound and outbound consignments to smaller, privately owned facilities.
A proactive inventory management system ensures a smooth flow of raw and subassembly materials throughout production and finished goods to reduce missed sales opportunities. An organisational-wide inventory system is adept at handling unexpected delays in supplier deliveries, preventing inventory shortages and extended lead times and allowing production schedules to remain on track.
Management risks can threaten an organisation's ability to achieve its goals. Commercial and operational risks are centred on an organisation's trading plans that may not turn out as originally planned. The risks refer to the possibility of an organisation needing to be more efficient in using its financial resources due to the uncertainties brought about by its failure to manage risk.
Organisations operate within an ever-changing environment and must constantly adapt and evolve to meet these changes. Low-performing organisations react to change least effectively, as they prefer to hire extra staff, rather than high-performing organisations, who look at how they operate to improve efficiency to negate the need to hire additional staff. Hiring staff is expensive and can lead to further inefficiencies if those staff add little organisational efficiency and profitability.
An organisation's most prominent issue is translating its strategic intent into the tactical and operational plans required to establish and achieve its goals and objectives. There is a perception that leaders only exist at the higher levels of management. However, a truly effective organisation understands that leaders exist at all levels of the management structure, critically translating a strategic vision into something the rest of the organisation will “buy” into.
To succeed in supplier relationships, it is essential to have a mindset of collaboration and be ready to tackle any obstacles that prevent organisational/supplier relationships from developing to their full potential. Through a proactive and cooperative problem-solving strategy, both parties can guarantee the delivery of best-in-class products and services that cater to their organisations' requirements. Supply issues must be resolved to benefit all stakeholders.
Throughout a product or service's lifecycle, it is essential to adapt management strategies to suit the evolving market landscape. By understanding the unique demands of each phase, organisations can make informed decisions to maximise profitability and ensure long-term success. Effective lifecycle management involves continuous monitoring, analysis, and adjustment to meet the changing needs and demands of the marketplace.
A team that purchases products and services on behalf of organisations to maximise customer service. Purchasing teams work to minimise the commercial risks of having excessive levels of capital tied up in inventory, whilst ensuring that the organisation meets its customer service strategy obligations. Purchasing maximises inventory availability and stimulates product and service innovation through supplier partnerships for the mutual benefit of its customers.
A quality management system (QMS) comprises processes and procedures to ensure services and products meet and exceed customer expectations. These systems are typically replicable and quantifiable and focus on ongoing enhancements. ISO 9001 illustrates a quality management system. QMS systems can deliver various advantages but take time to install. Introducing a QMS cannot fix an organisation lacking quality-focused leadership.
Organisations operate within an ever-changing environment and must constantly adapt and evolve to meet these changes. Hiring legal expertise is expensive and can lead to further inefficiencies if the advice sought or given adds little to organisational efficiency and profitability.
When forming a team, it is crucial to recognise that each member brings different skills, knowledge, experience, beliefs, and values. This diversity is a strength as it allows various perspectives to be considered in decision-making.
Supply Chain Management Made Easy:
Supply chains can vary in length and complexity depending on the specific industry they operate in. By allowing supply and demand to function independently, supply chains reduce costs, expedite economies of scale, and maximise productivity.
Commercial Management Made Easy:
Commercial risks are centred on an organisation's trading plans, which may not turn out as originally planned. Organisations that proactively research and adapt to evolving market conditions, such as enhancing their online presence, achieve greater success.
Procurement's primary responsibility is negotiating terms with suppliers to secure the best prices. This minimises the commercial, legal, and safety risks that can impact customer satisfaction and service delivery.
Operations Management Made Easy:
Translating an organisation’s strategic intent into tactical and operational plans is one of the most challenging aspects of today's evolving business landscape. Any disparity can significantly impede an organisation’s ability to achieve its objectives.
Copyright © Procurement and Supply Chain Management Made Simple - All Rights Reserved.